Agri-tech and machinery experts at Grimme, Agri-EPI Centre, Image Development Systems, Harper Adams University and The Centre for Machine Vision at the University of the West of England, Bristol have joined forces with two of the UK’s largest lettuce growers, G’s Fresh and PDM Produce, in the new Innovate UK-funded project to develop a robotic solution to automate lettuce harvesting.
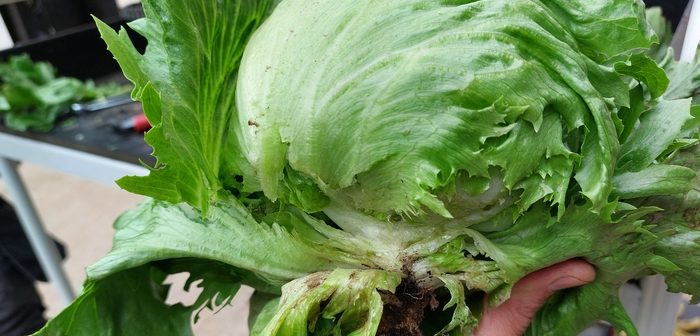
Whole head, or iceberg, lettuce is the UK’s most valuable field vegetable crop. Around 99,000 tonnes were harvested in the UK in 2019 with a market value of £178 million. But access to reliable seasonal labour has been an increasing problem, exacerbated by Brexit and Covid 19 restrictions. Early indications are that a commercial robotic solution could reduce lettuce harvesting labour requirements by around 50%.
Thom Graham, Vegetable Specialist at lead project partner Grimme said: “One of the greatest challenges facing the horticulture sector is sourcing sufficient seasonal labour to conduct their harvest commitments in a timely manner. In addition, rising cost of labour with no increase in retail price has squeezed margins. Growers are looking at solutions that can reduce labour input costs and maintain their resilience in the sector and we hope our expertise can help.”
Dermot Tobin, Managing Director of Farming at PDM said: “For many decades our business has relied on seasonal labour for harvesting lettuce. Nearly all the lettuce you see on UK supermarket shelves is cut by hand. Sourcing labour is getting really challenging and with wage inflation rising far quicker than return to grower prices margins are really tight. Our industry needs to embrace robotic technology to reduce our reliance on labour so being involved in this project is of the utmost importance to our business.”
Richard Ellis, Innovation & Research Project Manager of G’s subsidiary Salad Harvesting Services Ltd. said: “The process of lettuce harvesting has continuously evolved over the past 30 years, with harvest, packing, date coding, boxing and palletising all completed in the field, within minutes of the crop being cut. The cutting process of an iceberg is the most technically complicated step in the process to automate. We are encouraged to be involved and see the results of this project which offers the potential to reduce reliance on seasonal labour.”
The project will adapt existing leek harvesting machinery to lift the lettuce clear from the ground and grip it in between pinch belts. The lettuce’s outer, or ‘wrapper’, leaves will be mechanically removed to expose the stem. Machine vision will then identify a precise cut point on the stem to separate lettuce head from stem.
A prototype robotic harvester will be developed for field trials in England towards the end of the 2021 UK season, in around September, then at G’s Espana.
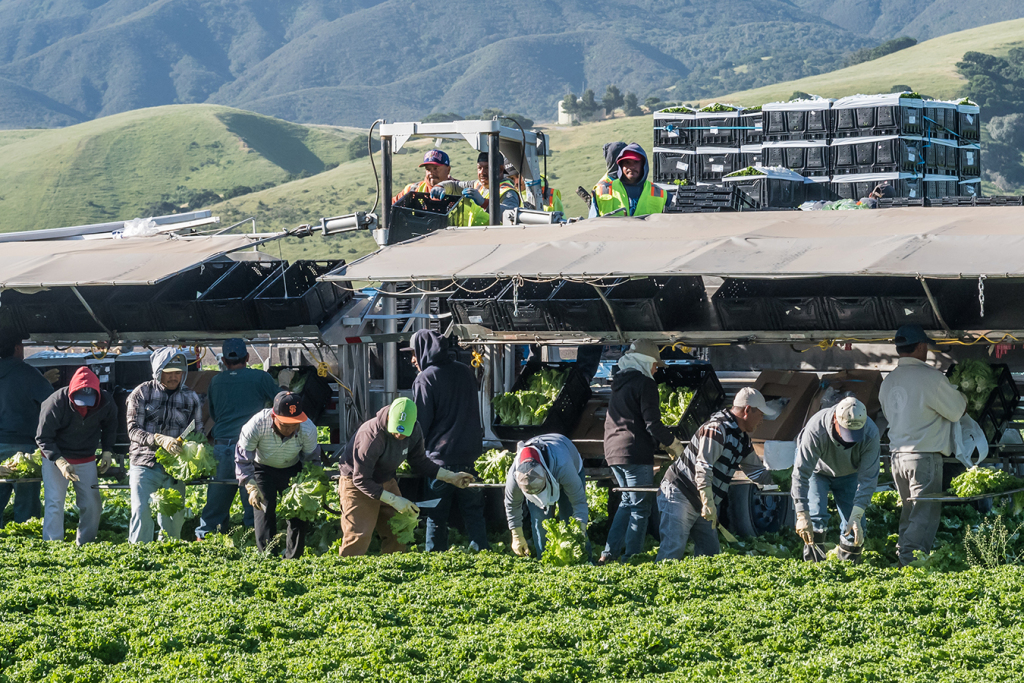
Lettuce is also a valuable crop in Europe and the US. 123,000ha of lettuce and chicory was grown in the EU in 2018[ii] with similar areas in the US. These areas have similar issues of access to seasonal labour, offering a significant potential market for the lettuce robot.
The Quality Challenge
- Early harvesters work best on whole-head bulk lettuce destined for salad plants and bagged salad products. They cut all the lettuce on an 80-inch-wide bed, lift the lettuce onto a platform where it is hand sorted and deposited into bins for transport to the processing plant.
- The quality standards for bulk lettuce are not as stringent as for fresh market lettuce, and these machines work well. However, the cost, speed, and capacity of the machines are important considerations for their use. Also, although this harvester eliminates the need for people to cut lettuce, you still need labor to sort and core it.
- Quality standards for fresh market lettuce are more demanding. And harvesters for this type of product are trickier to develop.