A Dutch robotics firm says its machine could be automatically harvesting greenhouse cucumbers in a few years.
Harvests for greenhouse cucumbers can run nine months to year-round with artificial light, said Richard Vialle, CCO and co-founder for One of A Kind Technologies. While the crop harvests can run around the year, an automated harvest could be more efficient and hygienic than traditional labor-intensive processes.
The prototype robot uses sensors to detect cucumbers hanging from a highwire greenhouse system and harvests them with a knife that is heated to reduce the transference of disease.
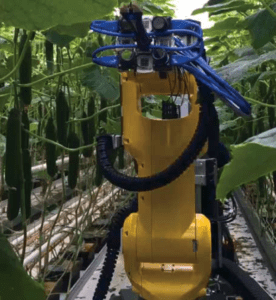
Vialle’s business group, which is marketing the technology under the Crux Agribotics brand, had a lot of interest from greenhouse cucumber growers after attending Fruit Logistica last February in Berlin. One of A Kind Technologies and its robotics brand Beltech have also developed an automated packing line for cucumbers and other vegetables.
Vialle said a harvesting robot is being developed to fit into “brownfield,” or existing, greenhouse operations.
Growers looking to make their greenhouses robotic would be making a big leap. Beyond investing in expensive technology, they would want to convert their operations from being open eight-10 hours per day to round-the-clock with less staff.
“We have to prove the solution,” Vialle wrote in an email. “The harvesting robots will still take two-three years to be launched to the market broadly. For the coming years, we will help the growers get used to automation that is more consistent, hygienic and less dependent on humans (which are becoming scarce, not consistent, costly and introduce viruses into the greenhouse environment).”
If not ready for commercial launch, the harvesting robot has proven the concept is possible.
“The prototype was built to prove, to ourselves and the value chain involved, that it is fundamentally possible to detect cucumbers, and the crops (leaves, branches) to subsequently classify the cucumbers to harvest only those cucumbers that match defined class types, and hence increasing the yield per square meter,” Vialle said. The machine combines a variety of technologies including two- and three-dimensional vision to see groups of cucumbers and plan routes to pick and remove them with minimal damage to the rest of the plant.
He said the company would like to test three to five robotic systems in different greenhouses over a very long period.
“Nothing fundamental, but it would be naive to paint a picture that it will be easy from now onwards,” he said. “We believe we can do it, it is now more an issue of funding and resources that need to be allocated.”
Currently, the sensors can identify about 99% of the cucumbers in a greenhouse, but even when the robot is finished, not all of the cucumbers will likely be accessible for robotic picking.
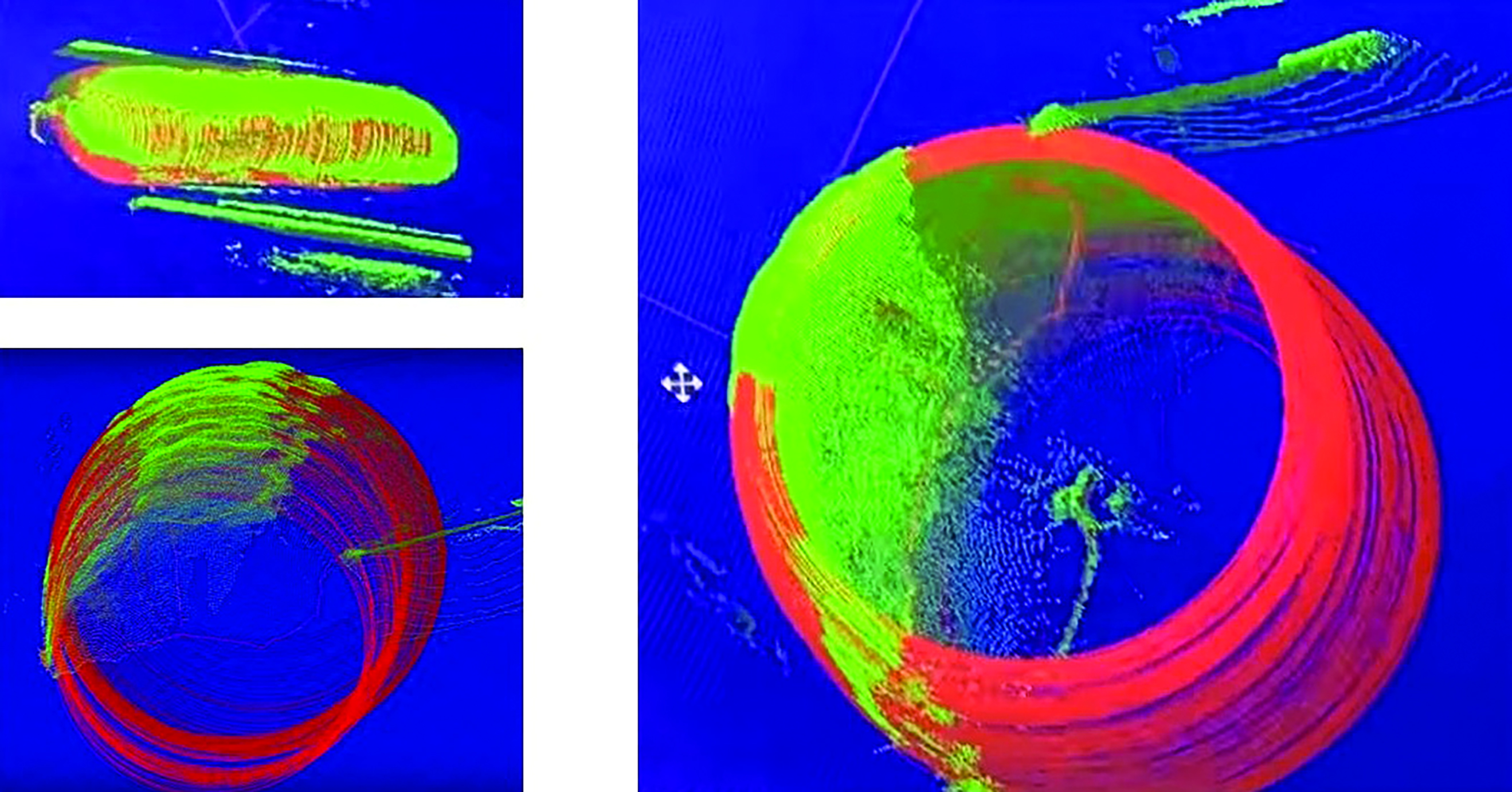
“We do not believe machine learning nor computer vision will be the limiting factor,” Vielle said. “It will be the maximum speed of movement by robots, picking and placing with preservation of the product quality and integrity (not damaging it externally, internally nor injecting stress into the plants).”
Like other agriculture technologies, the finished products could be marketed to growers as a service rather than a major equipment purchase. The business-speak terms for such arrangements are operational expenditure (OPEX), similar to the software as a service (SAAS) model.
“We will launch different robot concepts for grading, sorting and packing and offer these also in an OPEX model, where growers who are reluctant to invest in new technology can invest in a very limited way and pay the majority as they use (per packed box or tray),” Vialle said. “This service will include fully-managed services where we guarantee full warranty, on-site support, preventive and corrective maintenance and participate in the risk in a more balanced way. For sure, if the productivity is there, we make more money but can still offer growers a reasonable payback. Then, if they are convinced, they can buy the system still or keep it running as a service and get all these added-value services included according to contract.”
The group’s automated packing technology will be on display at the GreenTech show June 11-13 in Amsterdam. So far, the group gathered feedback at Fruit Logistica, a trade show that drew 78,000 trade visitors from 135 countries.
Agricultural labor, it seems, is not a problem only in the U.S.
“Growers all over the world confirm that we are working in the right direction driven by demographics (10 billion people, scarcity of resources), labor (scarce, costly, not consistent), urbanization combined with an increasing interest in environmentally-friendly handling (reducing waste of product and packages),” Vielle said. “Even relatively low cost-countries are seeing that the current model where humans are working in a sequential process is not scalable.
At the end, the work is also hard and dirty and people want, or get the chance to obtain, other work as well as the economy develops. In Holland, we see that the Eastern European temp workers are getting other jobs, and in the U.S., we hear similar things about the people from Mexico.”