A belt-fed mechanical system called PlantTape promises to reduce labor costs and save time during field planting.
The industry standard is rotary or carousel-style transplanters. But many small vegetable growers are also familiar with non-motorized, single-row mechanical planters fed by a system of paper pots, where transplants are grown in individual paper containers resting in a larger plastic tray. Connected by a paper strand, the individual paper containers peel away one at a time for mechanical planting in a single row.
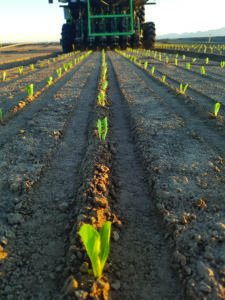
The PlantTape machine adds to that concept a power drive that can handle as many as eight planting rows at a time. Multiple trays can be staged for each row, too – strands of PlantTape from separate flats are strung together with biodegradable clips. The machine features a separate mechanical module for each row, and each module hangs close to the ground and plants in rapid fire.
“What we call the module is kind of the heart” of the machine, said PlantTape President Brian Antle. “It mimics a belt-fed machine-gun.”
The machine can hold 60 trays at a time, and each tray holds 810 plants. The spacing of the rows also is adjustable, and the total width of the machine plantings can vary from 60 to 84 inches.
In this fashion, a three-person crew – a tractor driver and two machine attendants – can plant 1.5 to 2 acres in an hour, Antle said. To match that pace using current methods, a grower would need two traditional planters with about 30 people, he said.
The PlantTape machine attaches to a tractor in a three-point system and is powered by the tractor’s hydraulic drive. Antle said the machine works well with a John Deere 6150 series tractor, and can be used to plant a wide variety of crops.
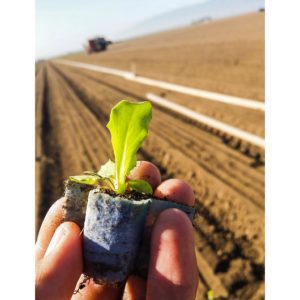
“As long as the seed can fit inside of the tape, you can grow damn near anything,” he said. “We’ve done some tomatoes, tobacco, melons, sugar beets, onions, leeks, bell peppers – we’ve done pretty much anything anyone’s ever thought of,” he said.
He added, though, that much of the current interest seems to be coming from western vegetable growers.
The technology was originally developed in Spain during the early 2000s, Antle said. It was acquired by Tanimura & Antle in 2014 for development in the United States.
Scott Rossi, who is the director of the internal farm at Tanimura & Antle, has been working with the machines for four years. He said that growers using switching from seed planting to transplants for the first time will have to adjust their patterns of sprays, water, fertilizer and bed prep – and closely watch the transplants once they’re in.
“You have to be open-minded,” he said. “You have to be willing to change.”
The group maintains a location in Spain, and this year, the group started commercial sales in North America. It’s also being used on a trial basis in Australia during 2018.
“We’re now selling machines and plants throughout North America,” he said. “There’s 25 being built right now and they’re all spoken for. Now it’s just a matter of building them quick enough to meet the demand.”
Antle said there’s roughly a six-week build time. The modules are manufactured in Spain, and the entire machine, including the chassis, is assembled in Oregon.
The machine costs from $100,000 to $200,000 depending on the number of modules in the machine – the number of rows the grower wants to plant. Machines run an average of $165,000, he said.
Another cost is the transplants themselves. A sowing device plants seeds and vermiculite into each pocket of the strand of tape, and then they must germinate and sprout, typically in a nursery setting.
“Currently, we’re selling the transplants just because we’re the only ones with the sowing line,” he said. Antle said the sowing line machines also are for sale; however, he declined to discuss pricing for those machines.
He said that so far, the reaction from growers has been strong.
“I think people are seeing this as the future,” he said. Paper pot systems like PlantTape make it easier to plant a wider variety of transplants. “Lettuce crops, you haven’t been able to grow from transplant very well because you can’t get the right root structure.”
PlantTape is also attractive to growers because of the reduced dependency on labor, Antle said.
“I don’t think anybody’s holding their breath to see the labor situation get any better.”
– Stephen Kloosterman, Assistant Editor
Above: Transplants are automatically planted in multiple rows by the PlantTape system. Photos: Brian Antle